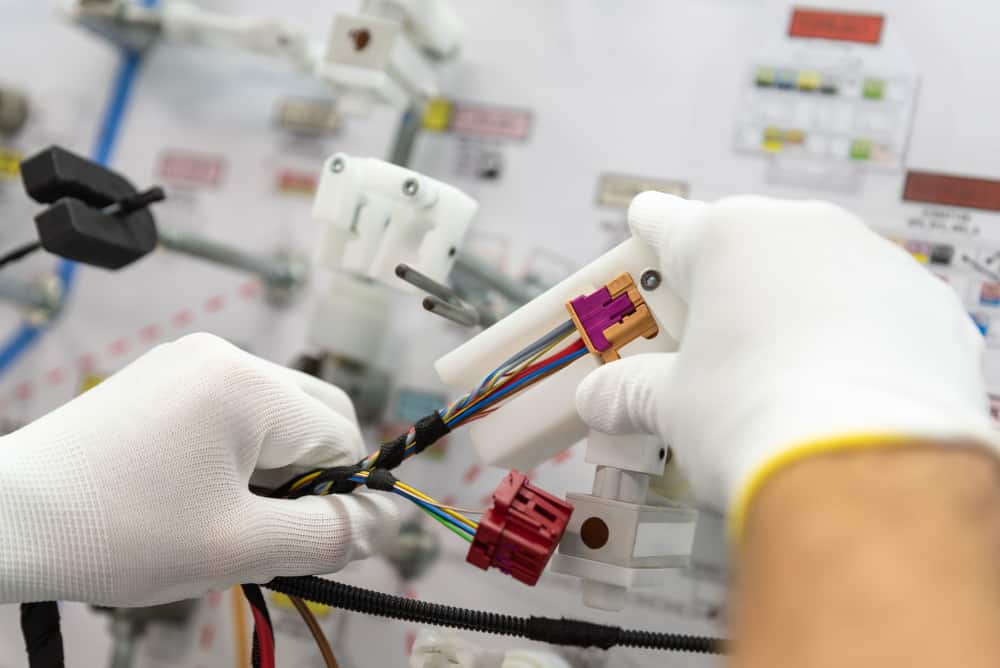
Wire Harness Assembly Process
Step Number |
Step Description |
Details |
1 |
Wire Preparation |
Wires are first cut to the required lengths using either manual cutters or automated wire cutting machines. The ends of the wires are then stripped to expose the metal conductor. |
2 |
Crimping Terminals to Wires |
Crimp terminals are attached to the ends of wires, which will assist in connecting the wires to their associated boards down the line. Crimping is usually achieved with a crimping tool or machine to ensure a secure and reliable connection. |
3 |
Inserting Wires into Connectors |
Wires with crimped terminals are inserted into their respective connectors. This may require specific tools or machines, depending on the connector type. |
4 |
Assembly of the Backbone |
The main cables are laid out and bundled together to form the backbone of the wire harness. This step might involve routing wires through protective sleeves or conduits. |
5 |
Branching Off |
Secondary wires or branches are connected to the “main backbone” at various points, according to the wiring diagram or schematic. |
6 |
Application of Protective Coverings |
Protective materials such as heat shrink tubing, specialized tubing, or tapes are applied to protect the wires and connectors from environmental hazards. |
7 |
Testing Each Connection |
Electrical tests are conducted to ensure each wire is correctly connected, and there are no shorts, opens, or miswirings. Continuity testers or multimeters are used here. |
8 |
Final Assembly and Securing |
The entire harness is assembled according to the layout, with all branches and connectors in place. Cable ties, clamps, or tapes are used to secure the harness structure. |
9 |
Quality Inspection |
The completed harness is inspected visually and through additional tests to ensure it meets all specifications and quality standards. Advanced testing may include dynamic stress testing to simulate environmental conditions (temperature cycling, vibration, moisture exposure) and ensure the harness’s longevity and reliability under operational stresses. |
Notes on Wire Harness Assembly Process Automation
In today’s world of automated PCB manufacturing, it’s worth noting that the wire harness assembly process still continues to depend on manual labor. Despite the potential for some degree of automation, the intricate nature of assembling wire harnesses and cable assemblies necessitates a hands-on approach. Crafting a wire harness involves numerous detailed and time-consuming tasks, making manual assembly not only necessary but also more cost-effective in many cases. Furthermore, the need for manual production in the creation of wire harnesses and cable assemblies is a result of their inherent need for customization. Wire harnesses are highly specialized components tailored to fit specific applications and larger systems and thus require manual craftsmanship in their assembly.Manual Labor Requirements in the Wire Harness Assembly Process
Manual labor plays a key role in wire harness production, especially for:- Threading wires through sleeves
- Applying fabric tape at necessary points like branch-outs
- Crimping terminals onto wires. When a single terminal must connect to multiple wires, multiple crimping operations are required
- Inserting sleeves into each other
- Securing wire strands with tape, clamps, or cable ties
Automation Use in The Wire Harness Assembly Process
While hand production is essential, it doesn’t completely exclude the use of automation and machinery in the manufacturing process. For instance:- Cutting machines are employed to cut wires to exact lengths
- Machines are utilized for crimping terminals or partially inserting wires with fitted terminals into connector modules
- Soldering machines seal wire ends
- Tools are used for twisting the wire
The Engineering Behind Wire Harnesses
- Engineers calculate the required gauge (thickness) of wires based on the current they need to carry and the length of the wire to minimize voltage drops and power losses. The layout must also consider the potential for electromagnetic interference (EMI), ensuring that sensitive signals are shielded or routed away from power lines to prevent cross-talk and interference.
- Conductors are typically made of copper or aluminum, chosen for their excellent electrical conductivity and flexibility.
- Insulation materials, such as PVC, polyethylene, or Teflon, are selected based on their electrical insulation properties, resistance to heat, chemicals, and UV light, as well as their mechanical durability.
- Protective sleeving adds another layer of protection against abrasion, moisture, and thermal extremes.
- Crimping, which involves deforming a metal connector to tightly grip a wire, relies on understanding material deformation and applying precise force to ensure a strong electrical and mechanical bond without damaging the wire.
- Soldering, used in some connections, involves melting a filler metal (solder) to join metallic surfaces, requiring knowledge of solder flow, wetting, and thermal management.