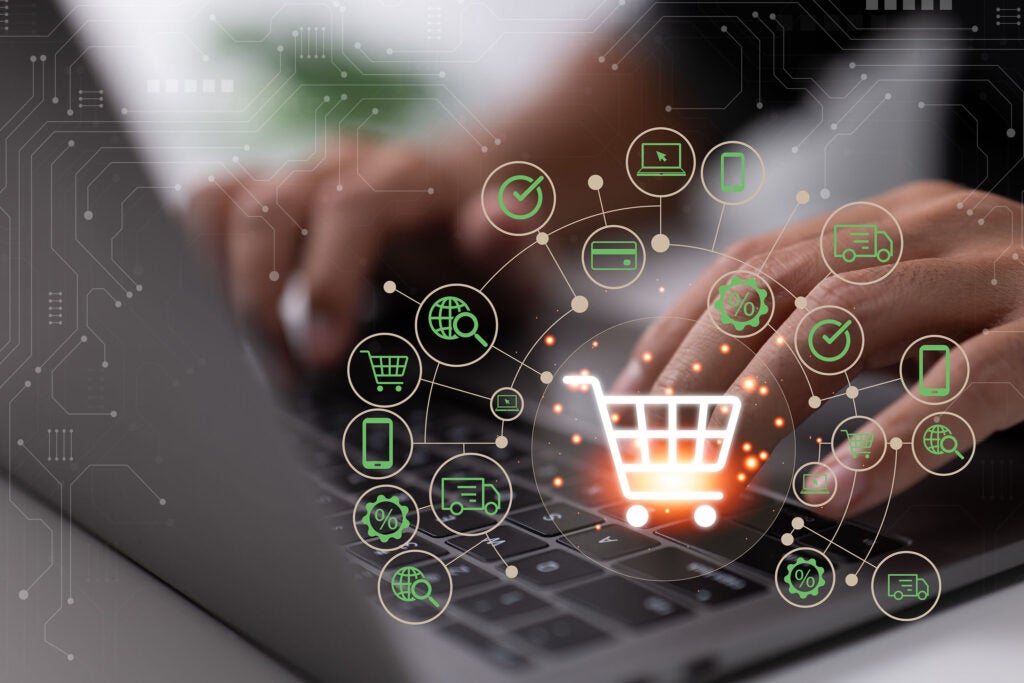
Once a PCB design is finished and ready for release, there may be nothing worse than finding out some parts are unavailable and cannot be ordered. This leaves you scrambling to find a suitable replacement part to get the design into production and may require design modifications. To prevent these issues, design teams should implement part multi-sourcing.
What is Part Multi-Sourcing?
Part multi-sourcing is the process of identifying and specifying multiple sources for parts upfront. This can be in the form of multiple vendors and distributors for critical components or multiple manufacturers for generic and common components.
Why Should You Leverage It?
Defining multiple purchasing options upfront with part multi-sourcing will ensure components are purchasable in the required quantity and timeline needed for PCB production. By incorporating part multi-sourcing during electronic component research and selection, you can:
- Prevent late-stage design changes due to single source part procurement issues
- Provide a known backup source for parts if needed
- Design in predictability and reliability to ensure your design stays on-track
While part multi-sourcing should be defined regardless of component management methodologies, to improve design efficiency, multi-sourcing data should be incorporated into your component library to reduce time spent researching parts for future designs.
How to Add Multi-Sourcing to Your Library and Part Introduction Process
When defining multiple sources for components, additional purchasing data must be gathered and documented including:
- Source
- Distributor
- Manufacturer
- Source Part Number
- Purchasing Information
- Cost
- Quantity on hand
- Lead time
Incorporating this multi-sourcing data adds another layer of complexity to manage within a component library. A common solution is adding multiple instances of the same part in the database; however, this can lead to several issues:
- Confusion on which part to use
- An expansive, hard to maintain library
- Only one purchasing option or source defined for each part in the database
The recommended approach to minimize confusion and streamline the component library is to create a relational database.
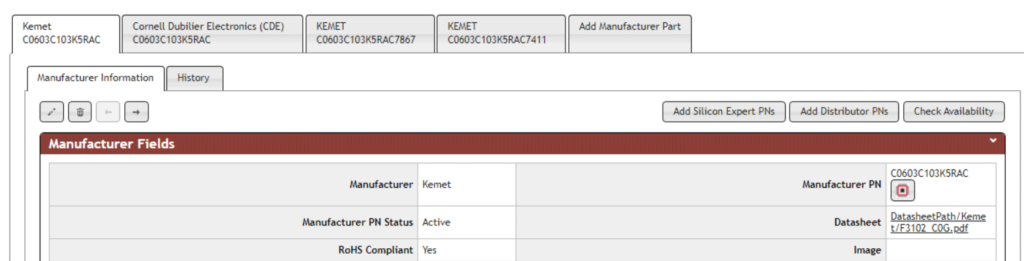
A relational database configuration allows users to link multiple manufacturers and vendors to a single part and creates a simplified environment. This process can be employed during the electronic New Part Introduction (NPI) process and/or to existing library components to create a robust, centralized repository of purchasable components.
Automate Part Muti-Sourcing with CIP
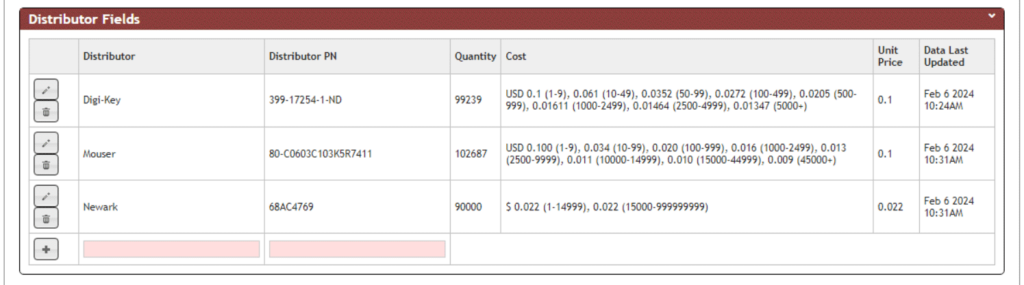
With supply chain delays and part availability a persistent problem, it is important to future-proof your designs to ensure manufacturing can continue uninterrupted for the duration of product deployment. Incorporating part multi-sourcing at the component database level, ensures supply chain resiliency as all parts selected for a design can be sourced to minimize delays and prevent late-stage redesigns. OrCAD CIP provides an efficient method to research and associate multiple sources to existing database components both during or after the NPI process. With OrCAD CIP, you can:
- View real-time pricing and availability from multiple distributors and manufacturers
- Easily find alternate sources directly in your CAD tool
- Quickly associate alternates to your parts with a just a few clicks
- Track and leverage alternate data in your designs easily
- Automatically add multiple purchasing options to BOMs
Learn how to automate multi-sourcing to create a future-proof, simplified component database and ensure successful part purchasing for your PCB designs with OrCAD CIP.