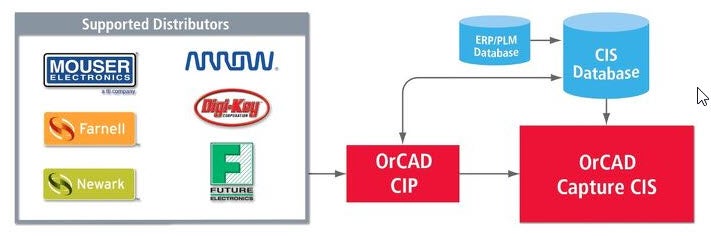
During the PCB design process, it’s highly improbable that all the parts required for the design are already found in your company’s part database due to the constant innovation of electronic components. For PCB components to keep up with industry and design standards, continuous improvement to be faster, smaller, and operate at lower power is required. This results in a consistent flow of new components to the market and your designs. Incorporating new components into a design or system is referred to as the electronic New Part Introduction (NPI) process. Throughout this process, many steps need to occur to ensure successful integration of new electronic components into a design:
NPI Step | Description | Responsible Party* |
---|---|---|
Define Component Requirements | Define the requirements of the new part including functionality, performance specifications, and specific features. | Designer |
Market Research | Identify suitable components that meet the defined requirements. Consider cost, availability, and compatibility with existing components. | Component Engineer or Designer |
Vendor Selection | Select reputable and reliable vendors to source components. Consider quality and lead times. | Component Engineer, Designer, or Purchasing |
Component Evaluation | Evaluate the selected components to ensure they meet the required specifications. May involve testing samples, reviewing datasheets, conducting simulations. | Designer |
Model Creation and Validation | Create schematic symbols and PCB footprints. Verify accuracy and integration between both. | Component Engineer or Designer |
Ensure Regulatory Compliance | Ensure components will comply with regulatory standards and certifications. | Component Engineer, Project Manager, or Librarian |
Add Component to Database | Enter all parametric information, models, supply chain data, and vendor information into the component database. | Component Engineer, Project Manager, or Librarian |
Release the Component | Verify all component information including parametrics, models, datasheets, vendors, and supply chain information then release the component for use in designs. | Project Manager or Librarian |
Design Integration | Integrate new components into the design. Update the schematic, layout, and documentation. | Designer |
Update Supply Chain Information | Update vendor information, lifecycle, and supply chain data to guarantee parts used in designs are available. This is an on-going task. | Component Engineer, Project Manager, or Librarian |
*Roles responsible for steps in the Electronic New Part Introduction (NPI) process may vary based on company standards and practices.
While the electronic NPI process is critical to design success, if performed inefficiently it often results in delays to the design process. After the designer requests a new part, the time it takes to create the associated models, perform part research, add the component to the company database, and verify the accuracy of component data can have a detrimental impact on time-to-market and project deadlines.
Electronic New Part Introduction (NPI) Process with OrCAD CIP
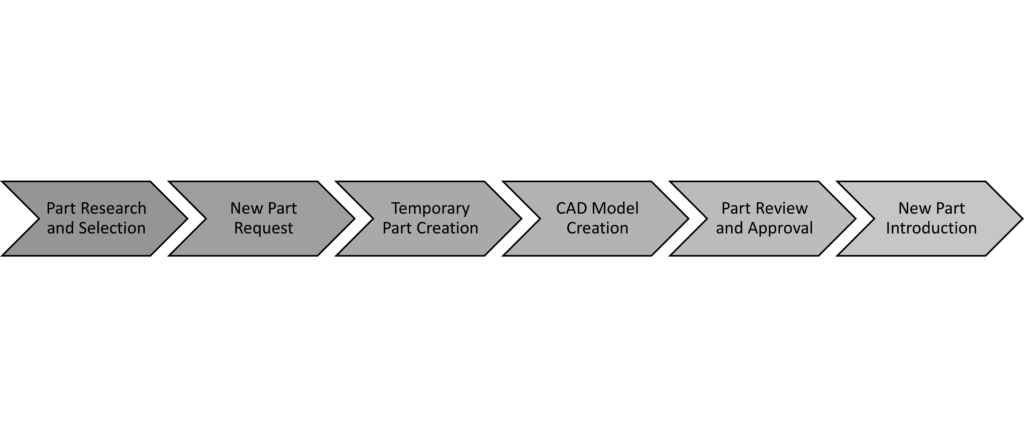
OrCAD Component Information Portal (CIP) streamlines the NPI process while creating a centralized library for part selection and management. OrCAD CIP provides direct integration to distributors and trusted data partners, allowing designers to research and select parts without leaving their CAD tool. When requesting a new part, parametric and supply chain information is pulled directly from distributors, saving time by eliminating manual entry and minimizing human-errors. A temporary part is generated while the part is reviewed and CAD models are created, allowing the designer to continue with the schematic. Customizable user roles and permissions coupled with automated alerts ensures the correct team members are editing and approving components while keeping the NPI process on track. With seamless integration between the project and the component database, designers are automatically notified of component changes or approvals and updates are applied as needed. While the electronic NPI process in OrCAD CIP greatly improves efficiency, there is still one hold-up – CAD model creation and verification.
Solving the CAD Model “Problem”
The complexity of today’s electronic components is necessary to meet the technological demands of cutting-edge products; however, this also increases the complexity of CAD model creation. With hundreds of pins and intricate device packaging, schematic symbols and PCB footprints can take hours if not days to complete. These models then need to be verified for accuracy and compliance to either company or industry (ANSI and IPC) model standards. In many product designs, 3D models and simulation models must also be created or sourced to achieve full system verification. To decrease the model creation and validation demands, component models can be sourced from reliable, CAD libraries such as Ultra Librarian. Typically, this involves searching the component model database, downloading the required models, and manually sharing the models with the CAD librarian or project manager; however, new integrated access to Ultra Librarian within OrCAD CIP automates this process.
Fully Automated Electronic NPI with OrCAD CIP and Ultra Librarian
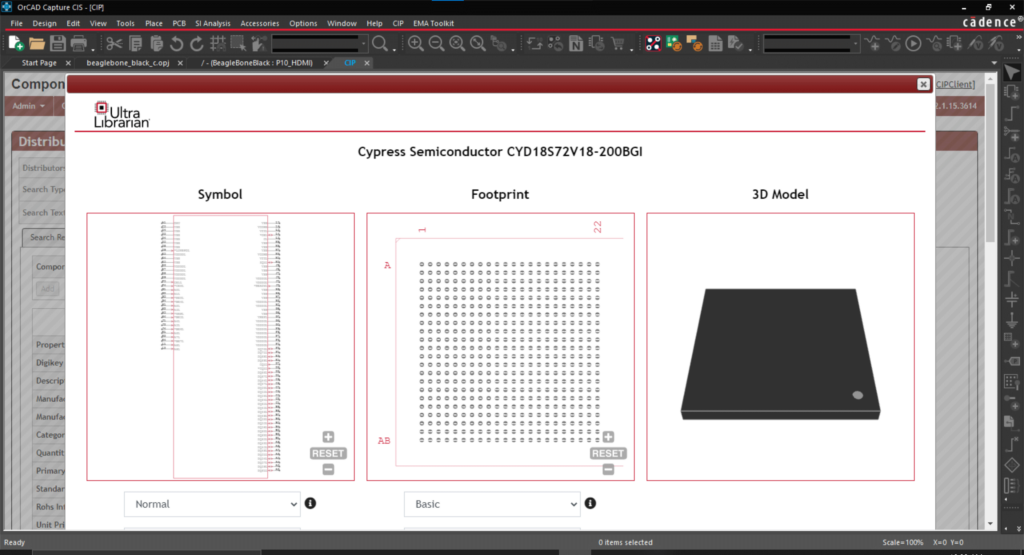
OrCAD CIP has now incorporated direct integration to Ultra Librarian within the electronic NPI process. During new electronic part requests, designers can now access, review, and associate fully validated component models. This allows design teams to achieve a fully automated and efficient NPI process with OrCAD CIP and Ultra Librarian by:
- Achieving an automated process to manage NPI from start to finish
- Performing part resource, selection, and addition directly inside your CAD system for ultimate productivity
- Accessing live distributor and supply chain data without leaving your design environment
- Continuing the design process while the new part is reviewed and approved with temporary parts
- Accessing pre-built, verified CAD Models through Ultra Librarian
- Easily associating CAD models to new parts
- Adding parts through a managed configurable process
- Eliminating error-prone manual entry of component parametrics
- Tracking new parts added with a detailed history
- Integrating with a PLM or other downstream systems
- Configuring user permissions, roles, and alerts to keep the NPI process on-track and ensure all stakeholders are informed
Learn more about the benefits of implementing a centralized part selection and management system with OrCAD CIP.